What we do
Since 1996 we solve problems around fluids, mainly water treatment. This we do in the industry, in big and small buildings and private homes with our Merus Ring.
The key word "solving" can be taken in the literal sense. In most cases it is not the water causing problems. If foreign substances in the water settle - for example in pipes or machines - the whole issue gets difficult and costly.
We advice and support you to get rid of limescale, corrosion or biofouling in your pipe. No matter how small or big your problem is.
By the way our alternative water softener is the hit.
Our Merus Ring
With the Merus Ring at the pipe the solubility of the soluble parts in the water can be increased.
This means for example: more limescale is soluble in the water and runs off with the water instead of blocking pipes and valves.
The trick here? We use the natural oscillation which is characteristic for every chemical substance. This can be changed to our benefit with superimposing waves.
This method of water treatment doesn't need further chemical additives in the water and no additional energy source is necessary. Without side effects it is ideal for drinking water as well as industrial water.
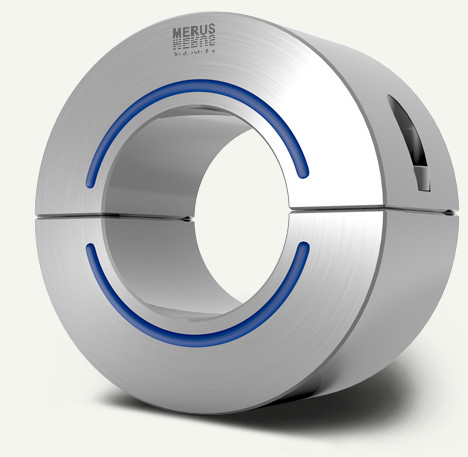
Merus for Biodiversity.
It is our belief that in our ecosystem water, air, earth and living beings are connected in a cycle. Since we are connected to the region in which we live and work, we make a small contribution to biodiversity by supporting a beekeeper. Without beekeepers, no bees - without bees nature and man suffer.
Everyone can do something for a healthy environment and plant flowers in the garden or, as far as possible, abandon pesticides in agriculture.